8 October 2025 | JW Marriott Grosvenor House Hotel
British Construction & Infrastructure Awards 2025 | Book your table now
The shortlist for this year's awards has been revealed, click on the link above to see who has made it. With nearly 250 entries across 24 categories from over 100 organisations, this year’s competition was fiercer than ever, making the judges' task especially challenging. From transformative projects to outstanding individuals, the 2025 finalists represent the very best in British construction and infrastructure.
The Awards for 2025 have been refreshed, along with the event name itself . They celebrate and honour the outstanding contributions of the British construction industry to society. This industry not only delivers transformative buildings and infrastructure that enhance lives and fuel economic growth but also creates exceptional job opportunities and careers, fosters strong community relationships, drives innovation, and champions the low-carbon agenda.
See who has made the shortlist for the inaugural Sir John Armitt Prize – This prize recognises projects that surpass objectives, satisfy clients, and deliver significant benefits to end-users and stakeholders. Winners embody industry excellence, showcasing what projects can achieve at their very best. This Prize will covet national media attention.
Sir John Armitt, Chair of the judging panel for the prize said:
“I am delighted to have been asked to help select the inaugural award in my name and celebrate the very best we can achieve. We design to satisfy a client’s desired outcomes. But at the same time, we need to satisfy wider stakeholders that we have created buildings and infrastructure which benefit the community and create an improved and uplifting environment. To achieve this, we must be creative, innovate, and challenge ourselves and our colleagues in a collaborative approach – and this award recognises a project team that exemplifies these very qualities.”
The awards take place on 8 October 2025, are brought to you by the Institution of Civil Engineers and New Civil Engineer and celebrate the hard work and dedication of the whole project team – from clients, architects, designers and contractors .
The awards take place on 8 October 2025. Guarantee your table now.
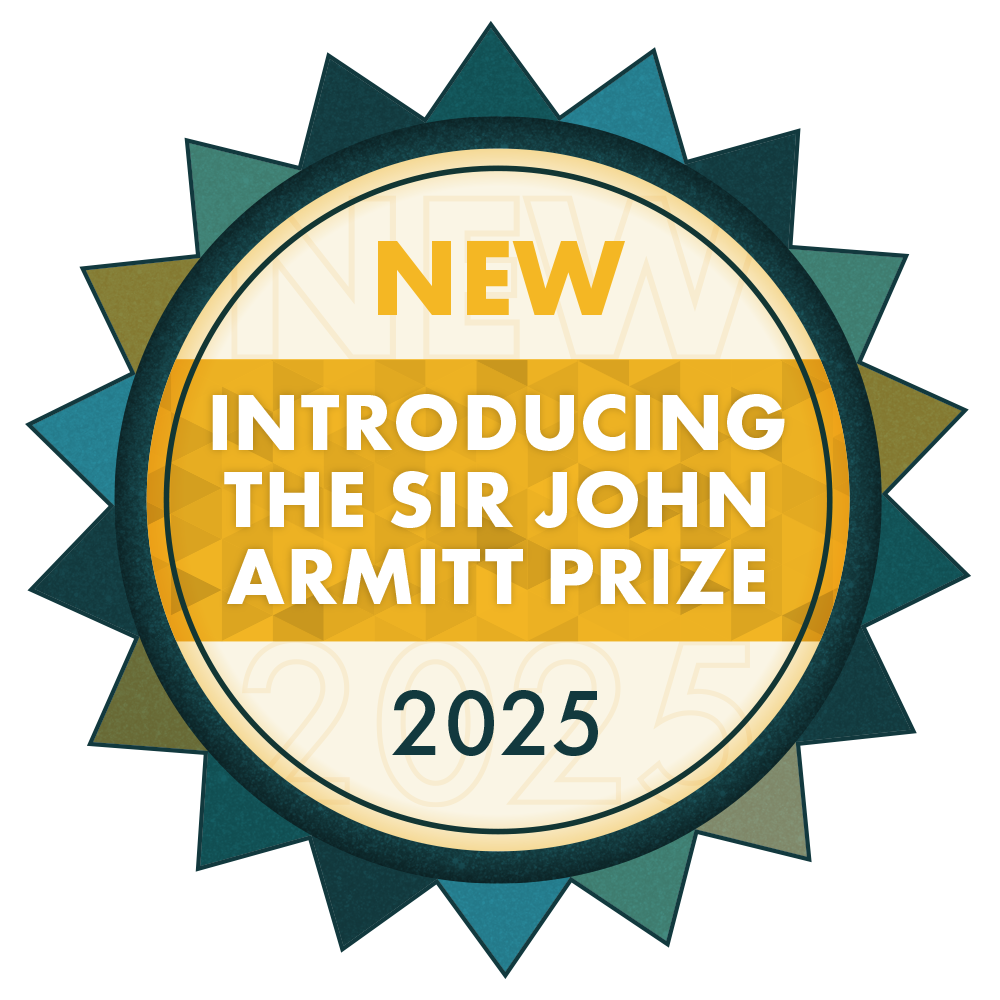
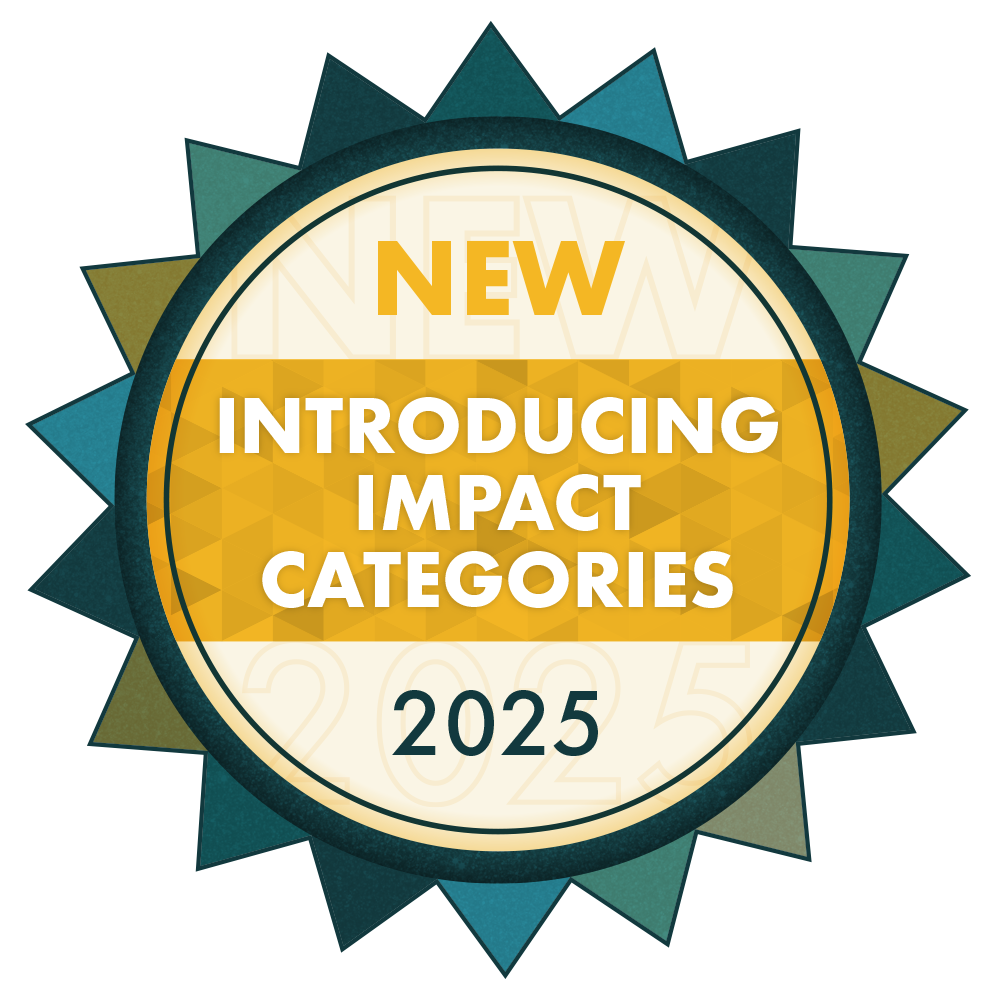
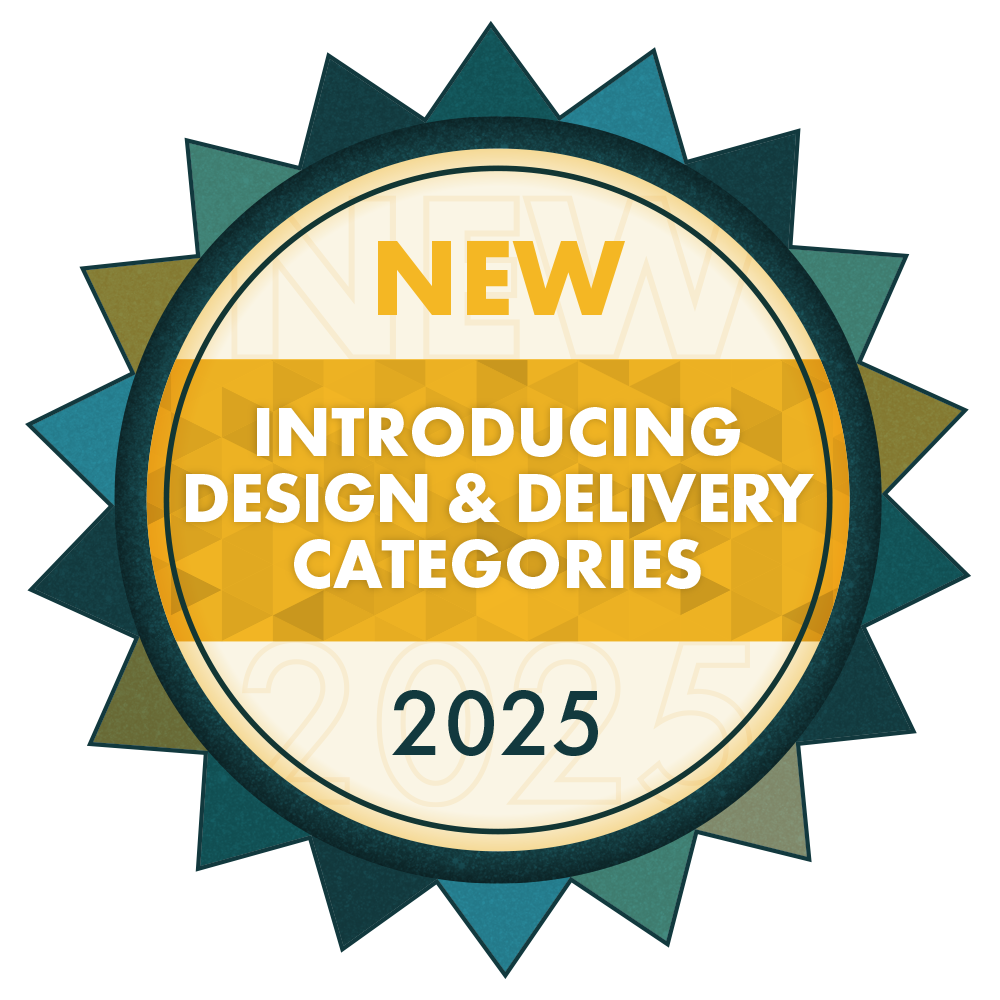
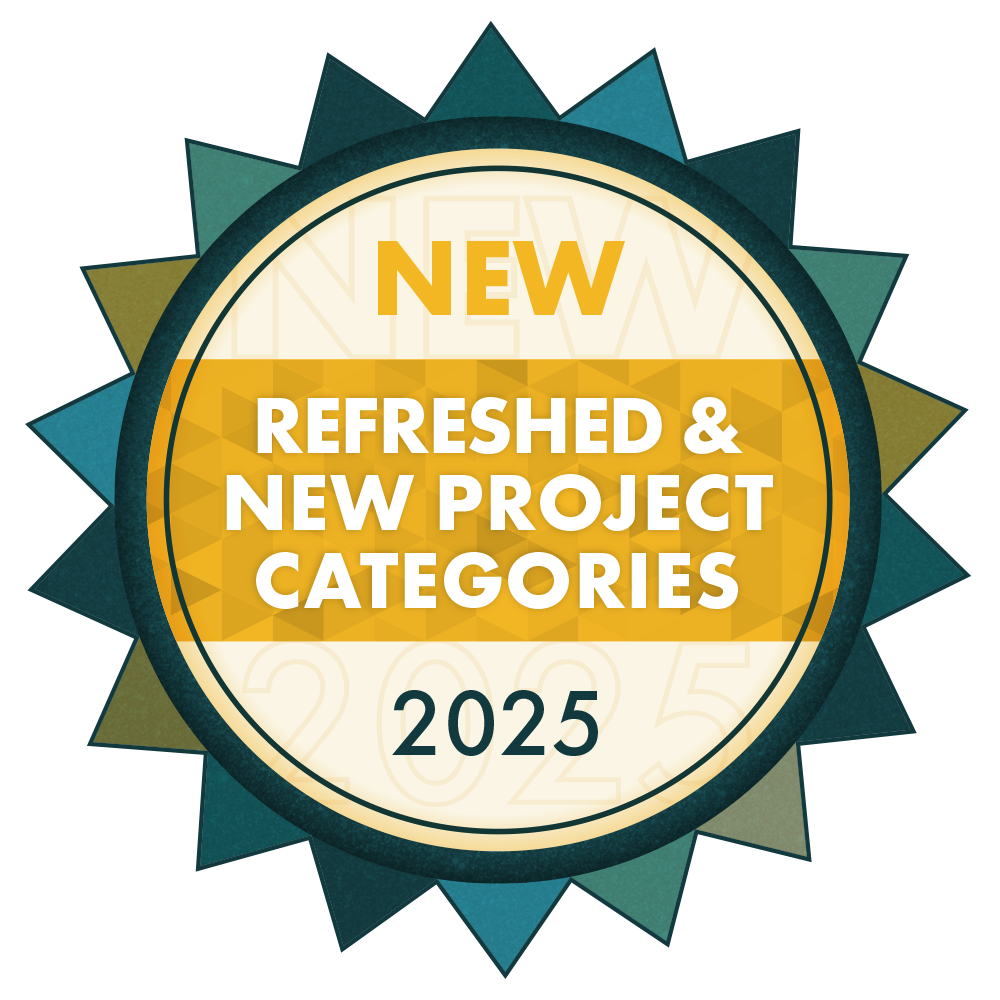